TH MATERIAL FOR BOWMAKING
In a previous article devoted to the comparison between ancient and modern bows, I advanced that the next topic would have been “the velocity of sound”. Thinking about it, I decided that before running, we better learn how to walk. Before explaining why the parameter of sound velocity quickness throughout the fibers is so important in bowmaking, I will try to describe the different woods that has been used during several time periods and which were the evaluation criteria that led to the choice of pernambuco as an irreplaceable material.

We can realize the big differences among bows of different periods just watching them carefully, we can notice that any development in the mechanic led to a change in the used material. The primitive bows, that had the sense of the curve in an opposite way compared to modern ones, were made of Bamboo and looked like a hunting bow. Of course the mechanic of these bows was very poor, the hair could be stretched by a hand but the instruments as well, the music and the concert hall owned very different peculiarities in comparison with the current ones.
To follow all developments, the bowmakers had to adjust the mechanic of the bow to match both the playing technique and the instruments. The musicians had to carry out more and more difficult passages and the concave curve didn’t allow this agility, furthermore the increased tension of the bow required some stronger material than bamboo. There was the need of an elastic material that could join a certain weight and thickness. The choice was on two particular woods as beech and snake wood.
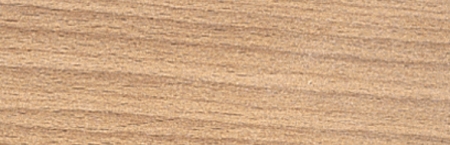
Beech wood
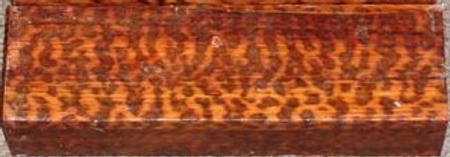
Snake wood
These two woods have similar properties that put them in a leading position among materials in a period that includes baroque and neoclassicism. Both woods are very thick, i.e. they have a very high specific weight and own a good elasticity. Both these properties were perfect for the use they were intended to and for the period they were used as material. The density is very high, the tannins gave to snake wood a very particular colour shade, gave the bows a very clear and smooth tone while their elasticity were high enough to satisfy the mechanical and sound requirements of those times.
These were the only wood used during the neoclassic period, until the greatest genius of all times in the bowmaking world, Tourte, made a visit to his friend – a fabric dyer and, almost by chance, he discovered the wood that would have been the “philosophical stone” of this field: Pernambuco wood.

Pernambuco wood: dark brown and light yellowish brown
Tourte realized that this new wood that he had in his hands was more elastic and with higher performance than snake wood. Comparing woods of same weight, thanks to the high fiber tension, it was able to develop three times more the sound and managed to launch it much further. Since 1975, year of the probable first use of pernambuco by Tourte, this wood is the only one used for high level modern bows.
I would like to add that Tourte has invented the modern bow just to exploit pernambuco properties at its best. You have to keep in mind that not only this wood has been the only one used but also that the modern bow didn’t need any further mechanical developments since then until nowadays.
Once he understood that this wood had no adequate replacement as material to make a bow, all makers had to face a new problem that was as difficult as the discovery of it: its selection. Even if pernambuco offers higher performances than any one else, inside this wood quality there are a lot of known species and the level of mechanical and sound output could differ a lot. During the year many selections criteria have been applied but until now they were all “empirical” i.e. based on intuition or non-proven logical way of thinking, just to name one there is a legend saying that the wood to be used in bowmaking has a very sharp acid taste.
You understood properly...a taste ! I Personally I saw a crazy guy that, in the third century, selected the material in a warehouse full of rats and spider nets literally licking pernambuco sticks ! Apart these craziness, during ‘800 and a part of ‘900, the selection criteria were the following ones:
Density : it was the first parameter to be taken into consideration. If the woodwas very thick, i.e. if its specific weight was a high one, it was selected because retained to own a rounder sound in comparison with a lighter one.
Color : the darker woods were preferred to the lighter ones, also basing this choice upon a psychological reason, as it was thought it could have a tone similar to its color
Force : the last and definitive parameter was the force of the wood and the choice was up to the bowmaker sensation. It is necessary to add a small corollary.
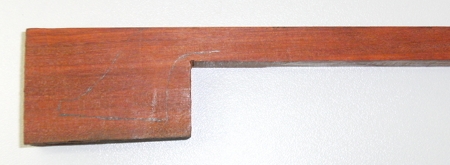
Pernambuco wood – brownish red
To understand if the wood was very strong or not, the bowmaker had to work on the stick almost until all the work was done, going on to take away wood until the wished force was reached. After that he weighted the stick and then decided what kind of bow had to be made out of it, If the stick was light but very resistant, its wood fibers were very nervous and so he could obtain an excellent bow; if the force was a good one but the weight was very high, i.e. the fibers had less tension , the bow will not have given out a good sound result. The most relevant example of this selection method for the material to be used comes from the French school that had the habit to mount excellent stick with gold, the medium levelled in silver and the poor ones in alpaca.
This last selection method, apart being very empirical as the previous two ones, was nevertheless the most reliable one; you could have afforded to find an excellent bow if made by a bowmaker with a good sensibility. The problem belonged to the maker, having to work on all selected wood until the finished stick and to find just two sticks out of ten tat could give good results. These represented a big problem for the hand-crafter that were compelled to work a lot , wasting their time for a small gain. Some of them realized while working that the lighter wood both in colour and shaded, set apart because considered not god enough, gave better final results than the heavier and darker quality. This problem gave birth to the research of a less empirical and more reliable evaluation method.
N. B. – The three Pernambuco sticks as per the picture shown in this page, have very different colours and weights. The dark brown stick has a medium density, the light brown one has a low density, while the red brown has a very high density, nevertheless the three of them are excellent and a day they will become fantastic bows. Both colour and density are no more considered reliable parameters, the tension of the fibers plays the major role, i.e. the most important parameter is the “ velocity of sound transmission ”
Velocity of sound transmission
After the first half of 1900, there was the start of the research for a scientific method that could allow the material selection without being compelled to work on it. The first attempts were made toward the Young module. The Young module is the coefficient of the maximum lost of nerve of the materials, i.e the limit after which the mechanical properties will be permanently affected. For instance, if you take a pernambuco table and place on two points at its both parts and you place a weight in the middle of it, the table will flex but if the weight is not strong enough to break the fibers, the table will regain its shape after the weight is removed. Increasing the overposed weight gradually, you will reach the utmost limit and the changing in the table will be permanent. That limit is the Young module expressed in kg/cm2.
This discovery of this innovative evaluation method brought great happiness but it didn’t last long, in a few time it was checked that ebony and pitch pine, i.e. both materials at the anthipodes, shown exactly the same Young module. The pitch pine, as we all know, is used for the harmonic table of violins because it is very light and its fibers have a high tension, while ebony is used for keyboards as it is very hard, it is very thick and has no vibrations.
The reason why such different materials own same parameters has to be found in the reason that the Young module gives no information about the elasticity of a material but just the breaking point of its fibers. Pitch pine fibers get very long before breaking, because they are very elastic, while those ones of ebony flex in a very slight way, but both of them break when the weight of 119 kg is reached.
To obtain a sure and scientific method to evaluate woods, reliable enough to give a bowmaker a certainty that wood to be used would have given excellent sound and mechanical result, we have to wait until 1982, when M° Giovanni Lucchi will apply a parameter that was used since long in another building fields: “the sound velocity”
After this long, hopefully clear, introduction we are finally able to afford the last phase related to the evaluation methods. Next week we will talk about the “the velocity of sound ”
So long.
Paolo
|